Enhancing Reliability with Diesel Generators for Fault Detection
Introduction
Diesel generators play a crucial role in providing backup power during outages and ensuring continuity in various industries and applications. These generators are relied upon to deliver consistent and reliable power supply, making their maintenance and fault detection essential to prevent unexpected breakdowns and interruptions. In this article, we will explore the significance of fault detection in diesel generators, the common types of faults that can occur, and the various methods and technologies available for detecting and diagnosing these faults.
https://www.lkpowerplant.com/product/quick-delivery-emergency-standby-power-400kw-silent-type-diesel-generator-set-for-peru/ of Fault Detection in Diesel Generators
The efficient operation of diesel generators is vital for businesses, industries, and critical facilities that rely on continuous power supply. Any unexpected failure or malfunction in a diesel generator can lead to costly downtime, loss of productivity, and potential damage to equipment. Fault detection plays a crucial role in ensuring the reliable performance of diesel generators by identifying issues at an early stage before they escalate into major problems.
Timely detection of faults in diesel generators allows maintenance teams to take corrective actions proactively, preventing costly repairs and minimizing downtime. By implementing effective fault detection strategies, organizations can enhance the reliability of their backup power systems and ensure uninterrupted operations during power outages or emergencies.
Common Types of Faults in Diesel Generators
Diesel generators are complex machines with various components that can experience faults and failures. Some of the common types of faults that can occur in diesel generators include:
1. Fuel System Faults: Issues related to the fuel system, such as clogged fuel filters, fuel leaks, or fuel pump failures, can disrupt the fuel supply to the engine, leading to reduced performance or engine shutdown.
2. Cooling System Faults: Problems in the cooling system, such as coolant leaks, overheating, or malfunctioning radiators, can cause the engine to overheat and result in damage to critical components.
3. Electrical System Faults: Faults in the electrical system, including faulty wiring, damaged connectors, or malfunctioning control panels, can impact the generator's ability to start, switch on, or deliver power to connected loads.
4. Battery System Faults: Issues with the battery system, such as low battery voltage, corroded terminals, or dead batteries, can prevent the generator from starting or operating efficiently.
5. Engine Mechanical Faults: Mechanical faults in the engine, such as worn-out pistons, damaged valves, or oil leaks, can lead to poor performance, increased fuel consumption, and engine breakdown.
Methods for Fault Detection in Diesel Generators
Detecting faults in diesel generators requires a combination of routine inspections, monitoring systems, and diagnostic tools to identify potential issues and anomalies. Some of the common methods for fault detection in diesel generators include:
1. Visual Inspection: Regular visual inspections of the diesel generator can help maintenance personnel identify visible signs of wear, damage, or leaks in various components such as fuel lines, hoses, belts, and connections.
2. Performance Monitoring: Monitoring the performance parameters of the diesel generator, including fuel consumption, oil pressure, coolant temperature, and voltage output, can provide valuable insights into the health and efficiency of the generator.
3. Oil Analysis: Conducting routine oil analysis can help detect potential engine problems, such as fuel dilution, coolant contamination, or metal wear particles, which can indicate internal issues with the engine components.
4. Vibration Analysis: Vibration analysis is used to detect abnormal vibrations or noises in the diesel generator, which could be indicative of mechanical faults, misalignment, or unbalanced components.
5. Thermographic Imaging: Thermal imaging technology can be used to detect overheating issues in the generator components, such as bearings, electrical connections, and cooling systems, by capturing temperature variations in real-time.
6. Remote Monitoring Systems: Implementing remote monitoring systems equipped with sensors and alarms can enable real-time monitoring of the diesel generator's performance and status, allowing maintenance teams to receive alerts and notifications in case of any abnormal conditions or faults.
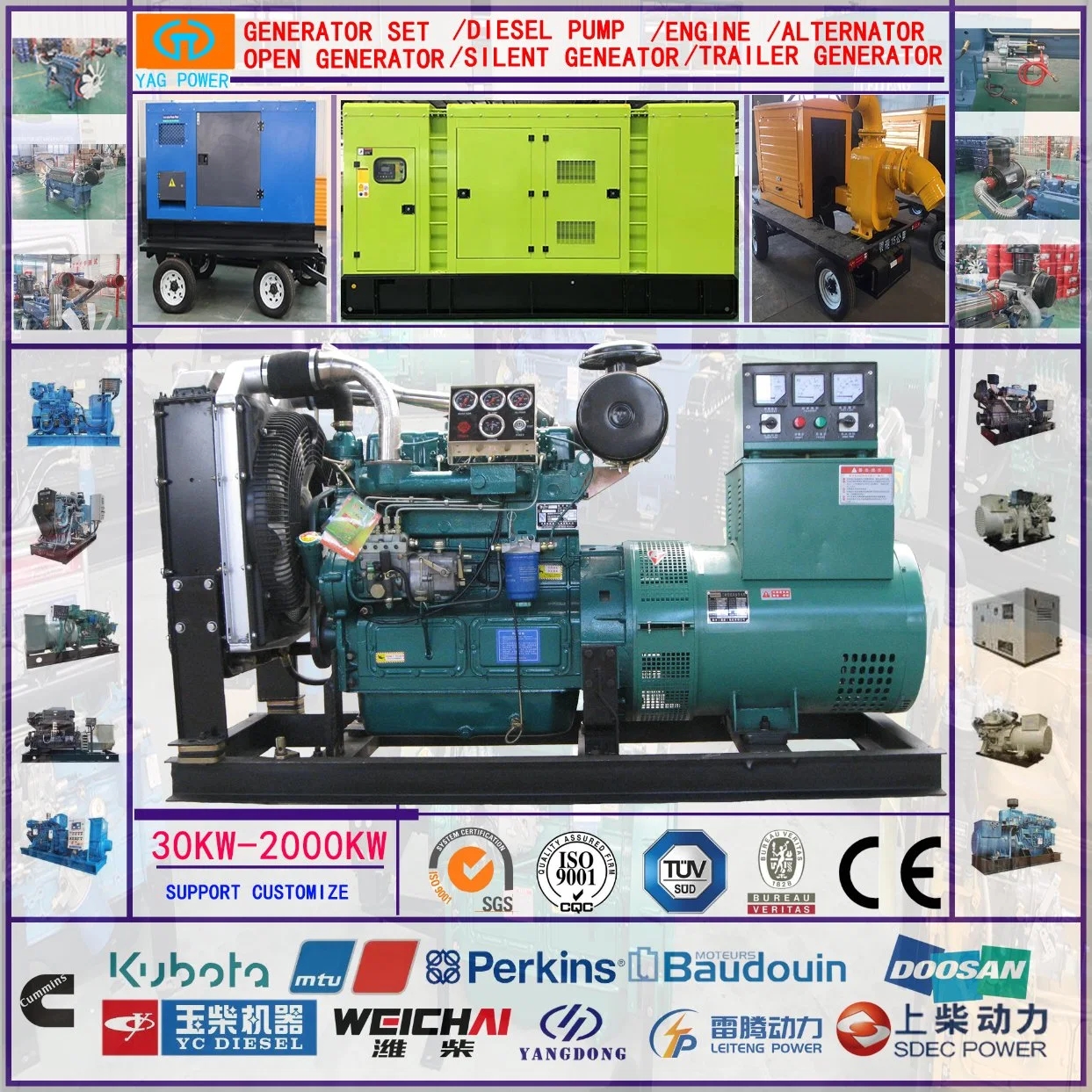
7. Diagnostic Tools: Utilizing advanced diagnostic tools, such as electronic control units (ECUs), diagnostic software, and handheld analyzers, can help diagnose specific faults in the diesel generator's engine, electrical system, or fuel system accurately.
Technologies for Fault Detection in Diesel Generators
Advancements in technology have led to the development of innovative tools and systems for fault detection in diesel generators, offering more accurate, reliable, and efficient ways to monitor and diagnose issues. Some of the key technologies used for fault detection in diesel generators include:
1. Condition Monitoring Systems: Condition monitoring systems utilize sensors, data acquisition units, and analytical software to continuously monitor the performance and condition of the diesel generator, detecting anomalies and predicting potential failures before they occur.
2. Predictive Maintenance Tools: Predictive maintenance tools leverage data analytics, machine learning algorithms, and predictive modeling to forecast potential faults in the diesel generator based on historical data, usage patterns, and operating conditions.
3. Internet of Things (IoT) Integration: IoT integration enables diesel generators to be connected to a network of sensors, devices, and cloud-based platforms, allowing real-time monitoring, data sharing, and remote diagnostics for proactive fault detection and maintenance.
4. Artificial Intelligence (AI) and Machine Learning: AI and machine learning technologies can analyze vast amounts of data from the diesel generator's operation, performance, and maintenance history to identify patterns, trends, and anomalies that could indicate potential faults or failures.
5. Remote Diagnostic Services: Remote diagnostic services offer real-time monitoring, analysis, and troubleshooting support for diesel generators, providing immediate feedback, recommendations, and solutions for addressing faults and issues remotely.
6. Blockchain Technology: Blockchain technology can be used to create secure, tamper-proof records of maintenance activities, fault reports, and repair histories for diesel generators, enabling transparency, accountability, and traceability of maintenance processes.
Benefits of Effective Fault Detection in Diesel Generators
Implementing effective fault detection strategies in diesel generators can yield numerous benefits for organizations, maintenance teams, and end-users, including:
1. Improved Reliability: By detecting faults early and addressing them promptly, organizations can enhance the reliability and availability of their diesel generators, ensuring continuous power supply and minimizing downtime.
2. Cost Savings: Proactive fault detection can help reduce repair costs, prevent major breakdowns, and prolong the lifespan of diesel generators, resulting in lower maintenance expenses and improved cost-effectiveness.
3. Enhanced Safety: Timely detection of faults in diesel generators can prevent potential safety hazards, such as overheating, fires, or electrical faults, ensuring a safe working environment for personnel and equipment.
4. Increased Efficiency: Fault detection enables maintenance teams to optimize the performance of diesel generators, improve fuel efficiency, and enhance overall operational efficiency, leading to better productivity and performance.
5. Regulatory Compliance: Maintaining reliable and properly functioning diesel generators through effective fault detection practices can help organizations comply with regulatory standards, industry guidelines, and safety regulations.
Conclusion
Fault detection in diesel generators is a critical aspect of ensuring the reliable performance, safety, and efficiency of backup power systems in various applications. By implementing proactive fault detection strategies, utilizing advanced technologies, and conducting routine maintenance activities, organizations can enhance the reliability of their diesel generators, mitigate risks of unexpected failures, and ensure continuous power supply during emergencies. Investing in fault detection capabilities not only improves the operational reliability of diesel generators but also contributes to cost savings, safety enhancements, and regulatory compliance for businesses and industries that rely on backup power solutions.